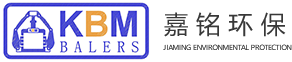
Iron press
The KHM series metal packing machine can extrude various metal waste materials (such as scraps, shavings, scrap steel, scrap aluminum, scrap copper, scrap stainless steel, scrap cars, etc.) into qualified furnace materials of various shapes such as rectangular, octagonal, cylindrical, etc.
It can not only reduce transportation and smelting costs, but also improve the speed of furnace operation. This series of packaging machines is mainly suitable for steel mills, recycling industries, as well as non-ferrous metal and ferrous metal smelting industries.
All models are driven by hydraulic pressure and can be manually operated or automatically controlled by PLC.
There are various ways to release packages, including flipping, side pushing, front pushing, and manual pickup.
Multiple models are available for selection: different pressures, material box sizes, and package block sizes and shapes.
In areas without power, diesel engines can be used as power sources.
Pressure iron machine parameters
MODEL | KHM-200 | KHM-300 | KHM-400 | KHM-500 |
Motor | 37KW | 45KW*2 | 45KW*2 | 45KW*2 |
Nominal Force | 200Ton | 300Ton | 400Ton | 500Ton |
Chamber Size | 1800*750*700mm | 2500*2000*1200mm | 2600*2000*1200mm | 2800*2000*1400mm |
Bale Size | 750*350mm | 500*600mm | 500*600mm | 500*600mm |
Bale Weight | 100~150KG | 400~700KG | 400~700KG | 500~800KG |
Operation | Manual/PLC automatic | Manual/PLC automatic | Manual/PLC automatic | Manual/PLC automatic |
outline drawing
Our services
Pre sales: (Professional level to earn customer trust)
·Maintain close contact with customers through multiple channels and understand their detailed needs
·Professional engineering personnel come to the site for precise on-site testing and explanation of product performance
·Provide the most comprehensive technical support for terminal and supporting customers, and scientifically and reasonably design the entire set
·Recommend energy-saving and cost-effective products to customers
·Share the latest industry news and promote new products
In sales (tabular progress makes customers worry free)
·The special person in charge follows up on the project and provides a tabular report, making it easier for customers to understand real-time progress
·Complete solutions/installation/foundation circle, establish close communication and contact with customer service providers
·Specialized personnel negotiate installation plans with clients to save installation costs and waste for clients
·Provide customized services based on different types of customers to meet their urgent needs
·The entire factory planning project is delivered in a tabular manner, with independent control over details and installation quality
After sales (humanized service to reassure customers)
·The after-sales service department provides 24-hour free hotline for customer service
·Provide online and offline guidance for customers to regularly maintain and repair equipment
·Regularly provide on-site inspection services for customers
·Archive customer device information and provide free accessory information
·Provide free device upgrade solutions, trade in services, and more